Fatal incident onboard a dive support vessel
A member has reported an incident in which a rigger was fatally injured when a large steel frame, known as a cursor, fell from a height of two metres trapping the rigger and resulting in fatal crush injuries to his chest. He was declared dead on arrival at hospital.
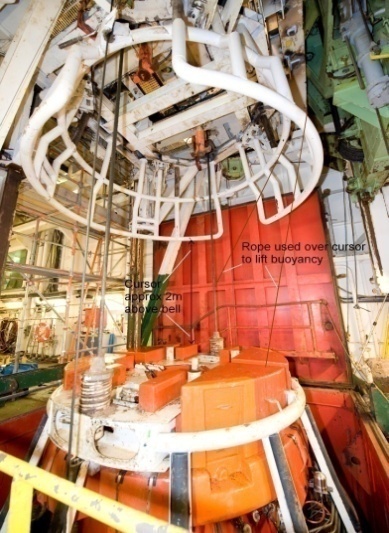
Work was being conducted onboard a dive support vessel (DSV) to modify the mode of operation of the cursor to ‘active mode’. An ‘active cursor’ is a frame that can independently be lowered, attach itself to the diving bell and be used to independently lift or lower the bell.
The work involved installation of a new hydraulic winch, structural modification and associated pipe-fitting. The workers involved with the modifications were experienced.
The cursor was suspended above the diving bell by the newly installed winch and it fell as a result of a failure of the hydraulic braking system for that winch. A rigger was working on top of the diving bell modifying some buoyancy units at the time of the accident. Although there were a number of other people in the vicinity and close to the worksite there were no other injuries.
The immediate cause of the winch failure was determined to be a faulty pilot valve in the cursor’s winch control system. A technical failure in the pilot valve prevented the automatic brake application on the winch.
Following investigation the company noted the following:
- A faulty pilot valve in the winch system failed, causing the brakes not to be applied in the stop position. This resulted in the hydraulic winch being unable to hold the weight of the cursor, which caused the winch to unwind and drop the cursor;
- There was no visual indication at the winch control panel that the brakes had been correctly applied, i.e. there was no warning system built into the hydraulic system by the manufacturer;
- Single point failure of this pilot valve had not been identified as a failure mode for the hydraulic system;
- The importance of the commissioning phases and interfaces for the hydraulic system and its control mechanisms were not sufficiently identified and were not appropriately managed;
- The control system was not fully commissioned prior to its use;
- The company’s own internal project management systems were not fully utilised;
- Communications and reporting lines within the project team and with offshore and onshore management were neither fully utilised nor understood;
- Design intentions and pre-commissioning requirements for safe operation of the new equipment had not been properly communicated to the work team;
- There was no secondary means of securing the active cursor;
- A decision was taken to work under the cursor. The hazard of working under a suspended load was not recognised as it was not a ‘typical’ load suspended from a crane.
The company drew the following lessons from the incident:
- There should be a clear and fully understood definition of the statement of requirements when dealing with external providers;
- External providers should provide clear pre-commissioning and commissioning guidelines and follow them during commissioning;
- Project management for ‘internal’ company projects should be to the same rigorous standard as applied when managing client projects. In particular, personnel competency requirements should be rigorously applied for all project management;
- There should be a clear definition and understanding of the responsibilities and reporting lines of those managing such work both on and offshore. Lines of responsibility between vessel-based personnel and shore-based staff should be fully agreed and understood prior to commencing the work onboard;
- All safety management tools, such as behavioural observations, toolbox talks, risk assessments, time out for safety etc., should all be working as planned;
- There should be adequate ownership, supervision and intervention of all ‘projects’ onboard the vessel through onboard review meetings and safety intervention tools. This is particularly important when operating conditions are subject to change, as during installation, commissioning, trials and harbour activities;
- Structured review such as failure modes and effects analysis (FMEA) and both internal company approval and external approval should be obtained before commissioning hydraulic and other complex safety-critical systems;
- The change from commissioning phase to operational phase must be clearly defined, particularly for safety critical equipment. Personnel should not make assumptions about the integrity of equipment before it has been formally accepted as operational;
- Measures should be in place to identify and mechanically secure suspended loads before passing beneath.
There are clear lessons to be learnt relating to personnel competence, project management, communications and lines of responsibility, supervision, utilisation of procedures and risk awareness. This incident highlights the importance of making sure that all the systems and controls in place to act as barriers and prevent an accident should be properly maintained and proven to be working at all times.
The specific barriers that failed to prevent this incident were:
- Project controls – these should be robust and always utilised for internal as well as external projects;
- People selection and development – competence schemes should fully operational and effective;
- Technical integrity – there should be robust design and effective equipment quality control;
- At a practical and basic level the final barrier which should always be in place, and which was not in this case, is: Always be aware of the surroundings, look out for ‘non-obvious’ suspended loads; and
- Never work under a suspended load – and challenge others who do!
Safety Event
Published: 22 December 2009
Download: IMCA SF 18/09
IMCA Safety Flashes
Submit a Report
IMCA Safety Flashes summarise key safety matters and incidents, allowing lessons to be more easily learnt for the benefit of all. The effectiveness of the IMCA Safety Flash system depends on Members sharing information and so avoiding repeat incidents. Please consider adding safetyreports@imca-int.com to your internal distribution list for safety alerts or manually submitting information on incidents you consider may be relevant. All information is anonymised or sanitised, as appropriate.
IMCA’s store terms and conditions (https://www.imca-int.com/legal-notices/terms/) apply to all downloads from IMCA’s website, including this document.
IMCA makes every effort to ensure the accuracy and reliability of the data contained in the documents it publishes, but IMCA shall not be liable for any guidance and/or recommendation and/or statement herein contained. The information contained in this document does not fulfil or replace any individual’s or Member's legal, regulatory or other duties or obligations in respect of their operations. Individuals and Members remain solely responsible for the safe, lawful and proper conduct of their operations.