Explosion causing fatal injury during maintenance of Metocean buoy
A member has reported an incident in which a crewman was fatally injured during the recovery and maintenance of a metocean buoy, after it had been in use in-sea for a period of around two years. The incident occurred after the buoy was recovered onto a service vessel for cleaning. After retrieval onto the service vessel, the buoy was cleaned, and the task of opening the instrument compartment started. This compartment also held the lead-acid battery packs of the buoy. Access was gained by removing a circular lid secured by 16 bolts. The removal of the bolts had been completed, except for the last bolt which proved to be seized. The decision was made to free this bolt using an angle grinder.
Only moments after applying the grinder, an explosion took place which resulted in the lid blowing open and the instrument modules and their mounting plate being projected outwards with great force. These items struck the crewman, causing him to be fatally injured.
The buoy had a discus shaped hull that could be split in two to ease transportation. A keel with counterweight was mounted under the hull to stabilise the buoy. A cylinder in the middle of the hull contains all electronic modules, the power package and the wave sensor. The different electronic modules were mounted into special splash proof compartment boxes to secure safe handling of the sensitive electronics. The buoy was equipped with a mast to support the meteorological sensors and the communication antennae. The dimensions in the diagram below are in millimetres.
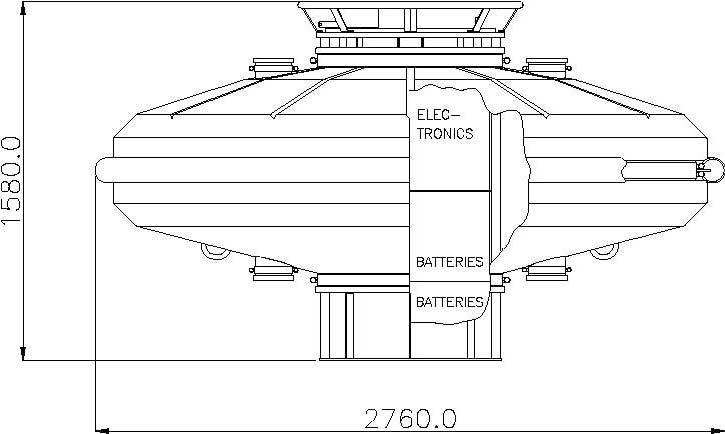
The immediate cause of the explosion was found, on investigation, to be sparks from the grinder igniting an explosive mixture of hydrogen and oxygen which had built up inside the compartment. The hydrogen build-up was assumed to stem from the lead-acid batteries. The lead-acid batteries contained in all metocean buoys of this sort are of the so called valve regulated type, meaning that they are sealed, except for a pressure relief valve. These batteries feature a built-in gas recombination system, and the small amounts of gas released through the valve pass through an additional catalyst before being conveyed to the outside of the buoy. This system is intended to prevent any build-up of hydrogen. The final technical investigation showed no sign of malfunction of the battery venting system.
The root cause of the incident was determined to be to a combination of lack of maintenance and a failure to follow existing procedures. The investigation concluded that the following chain of events led to the hydrogen build-up, and eventually the accident.
- Corrosion around lid sealing due to bird droppings and rain or sea spray caused the sealing to fail;
- Water, sea salt and bird dropping (guano) ingression into the instrument compartment past the leaking lid sealing;
- Corrosion and subsequent volume increase on details of battery rack due to ingression;
- Increased pressure on batteries from rack, resulting in cracked battery cases;
- Hydrogen build up due to one or more of these effects;
- Corrosion of aluminium, accelerated by guano and sea salts dissolved in water;
- Corrosion due to spilled battery acid from cracked batteries;
- Gas leakage from cracked battery cases;
- Hydrogen escapes due to leaking lid sealing and increasing temperature;
- Grinder ignites hydrogen.
The following further points were noted:
- The existing user documentation for these metocean buoys states that the buoys have to be purged before opening the lid to the instrument compartment. The buoys incorporate valves to allow for this procedure. In this incident this procedure was not followed;
- There was a warning in the manual against ignition sources;
- There were instructions in the manual on purging the instrument compartment;
- A protective cover over the instrument compartment lid and also bird spikes (to prevent birds landing on the buoy) were available and were to be fitted at that time.
The following actions were taken:
- Improvements to warning signs and clearer instructions were developed, and also improved designs for the instrument compartment and battery rack;
- Development of clearer instructions, which emphasize that at all times the buoys should be treated with the assumption that they could contain an explosive gas mixture.
The following precautions have now been identified:
- Exercise particular care with buoys that have not operated normally in the period prior to retrieval;
- Equalise the pressure inside the buoy to the ambient air pressure by opening the gas filling valves;
- Purge the interior of the buoy with air or nitrogen in order to remove any possibility of hydrogen gas, using the procedure described in the user manual;
- Do not allow any ignition source -including power tools -near the buoy until it is fully opened;
- Maintain a safe distance. Only the minimum required number of persons should be in the vicinity of the buoy until it is fully opened. Never stand in direct line of the instrument compartment lid;
- When flushing has been completed, proceed immediately with the opening of the lid;
- Leave the lid fully open for a further 10 minutes.
Safety Event
Published: 4 April 2013
Download: IMCA SF 05/13
IMCA Safety Flashes
Submit a Report
IMCA Safety Flashes summarise key safety matters and incidents, allowing lessons to be more easily learnt for the benefit of all. The effectiveness of the IMCA Safety Flash system depends on Members sharing information and so avoiding repeat incidents. Please consider adding safetyreports@imca-int.com to your internal distribution list for safety alerts or manually submitting information on incidents you consider may be relevant. All information is anonymised or sanitised, as appropriate.
IMCA’s store terms and conditions (https://www.imca-int.com/legal-notices/terms/) apply to all downloads from IMCA’s website, including this document.
IMCA makes every effort to ensure the accuracy and reliability of the data contained in the documents it publishes, but IMCA shall not be liable for any guidance and/or recommendation and/or statement herein contained. The information contained in this document does not fulfil or replace any individual’s or Member's legal, regulatory or other duties or obligations in respect of their operations. Individuals and Members remain solely responsible for the safe, lawful and proper conduct of their operations.