High potential near miss: working on pressurised pipeline
What happened?
During the dewatering of a 6” flexible jumper, a near miss incident occurred when the pull head was removed whilst it was still under pressure. This resulted in a foam pig that was inside the flexible jumper being unexpectedly ejected by the residual pressure. The pig narrowly missed personnel in the immediate vicinity and landed on the ground approximately 2m away from the jumper end.
The incident had the potential for serious injury to personnel standing in the line of fire. Activities were being controlled and supervised by our member at a third-party worksite.
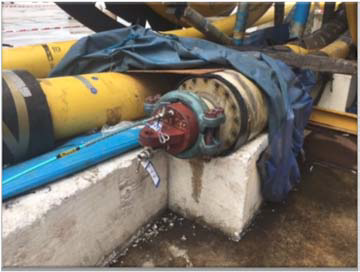
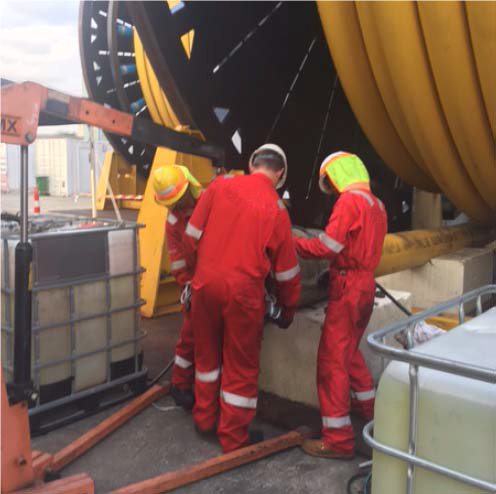
What went wrong? What were the causes?
Our member noted the following:
- The approved procedure for the pressure testing and dewatering activities was not followed correctly (a vent valve that should have remained opened at the other end of the jumper was closed);
- A ‘working copy’ of the approved procedure was not available at the task location for reference by personnel;
- There was no on-going sign-off being conducted as each task was completed;
- There was no check conducted for positive confirmation that the system was at ambient pressure before starting to remove the pull head to access the foam pig;
- There was no requirement for formal sign-off/handover of system control from the pre-commissioning services company to our members’ personnel who were required to remove the pull head for the foam pig inspection.
What actions were taken? What lessons were learned?
- When lines have been pressurised, isolation and venting processes should be in place, which ensure the ambient pressure is verified before breaking pressure containment;
- Supervision on worksites should highlight safety critical points within the procedures and ensure that they are strictly followed by personnel;
- Where stored pressure or energy is involved, ensure approved procedures contain requirements for formal sign-off/handover of system control, particularly when third party sub-contractors are involved.
Members may wish to refer to the following:
- High potential stored energy incident: inner buoyancy module clamp failure during removal (a casual factor being failure to properly manage the task)
- Fatality: Stored pressure release
Safety Event
Published: 23 August 2018
Download: IMCA SF 18/18
IMCA Safety Flashes
Submit a Report
IMCA Safety Flashes summarise key safety matters and incidents, allowing lessons to be more easily learnt for the benefit of all. The effectiveness of the IMCA Safety Flash system depends on Members sharing information and so avoiding repeat incidents. Please consider adding safetyreports@imca-int.com to your internal distribution list for safety alerts or manually submitting information on incidents you consider may be relevant. All information is anonymised or sanitised, as appropriate.
IMCA’s store terms and conditions (https://www.imca-int.com/legal-notices/terms/) apply to all downloads from IMCA’s website, including this document.
IMCA makes every effort to ensure the accuracy and reliability of the data contained in the documents it publishes, but IMCA shall not be liable for any guidance and/or recommendation and/or statement herein contained. The information contained in this document does not fulfil or replace any individual’s or Member's legal, regulatory or other duties or obligations in respect of their operations. Individuals and Members remain solely responsible for the safe, lawful and proper conduct of their operations.